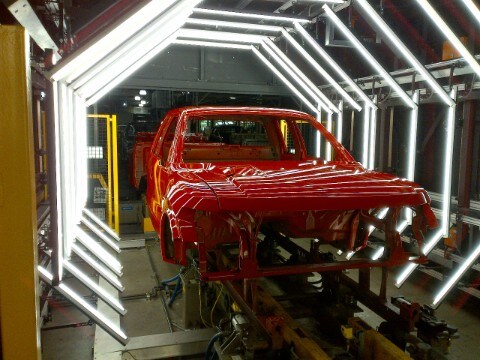
- Industry-first dirt detection technology uses high-resolution cameras to generate a 3D model so Ford can identify and eliminate dirt particles smaller than a grain of salt on vehicle paint surfaces
- Ford data show new automated vision system led to an 82 percent improvement in combined paint quality and customer satisfaction metrics for surface finish within one year
- Digital imaging system analyzes more than 3,000 images in 15 seconds to identify dirt particles. Previously, paint inspections were based solely on the human eye
- This year, the dirt detection technology launches at three more Ford assembly plants in North America, followed by two additional assembly plants in 2014
Here’s the dirt on Ford’s new paint technology: There isn’t any.
New Ford F-Series models are the latest vehicles to benefit from the company’s industry-first dirt detection technology to ensure optimal paint and surface quality. The system uses high-resolution cameras and reflected light to digitally identify surface imperfections finer than a grain of salt in final vehicle assembly, and to cue operators where to polish and buff out imperfections.
By using dirt detection technology, Ford improved paint quality and reduced customer complaints of vehicle surface finish by 82 percent within one year, as measured by customer warranty data for F-Series models produced at the company’s Dearborn Truck Plant in Dearborn, Mich.
“This system ensures better paint jobs and surface finishes for Ford customers around the world,” said Tom Dougan, project manager, global paint applications at Ford.
How it works
Ford’s dirt detection technology takes microscopic scans of each painted vehicle surface, and then cues final assembly operators to address repairs where necessary. In the past, paint and surface inspections were based on human-eye examination.
The 3D imaging system applies varying degrees and angles of light while scoping the paint surface of vehicle bodies to identify dirt in paint and other irregular paint conditions. High-resolution images – 3,150 images are captured in 15 seconds for every vehicle made – are stitched together for a full 3D image that is digitally compared to a perfect computer model.
The dirt on the dirt
Dirt particles in paint are difficult to manage with conventional quality control methods. Minute particles can enter a shop floor from multiple environmental sources, machinery or workers, which makes paint quality one of the toughest variables to control in production. Along with Dearborn Truck Plant, the automated inspection system is now being used in the United States at Ford’s Kentucky Truck Plant.
“This is one of the most exciting integrations of optical science and digital technology in the automotive industry,” said Dougan. “By combining innovations in vision technology, processing speed and software, Ford continues to invent new technologies that give our customers better paint quality and surpass competitor offerings.”
Locations
Globally, dirt detection technology is used at three Ford assembly plants. Here are the plants and the vehicles built there:
- Valencia Assembly Plant, Valencia, Spain: Ford C-MAX (Grand C-MAX and compact models)
- Dearborn Truck Plant, Dearborn, Mich.: Ford F-Series
- Kentucky Truck Plant, Louisville, Ky.: Ford Expedition, Ford Super Duty
The technology launches later this year at these plants:
- Louisville Assembly Plant, Louisville, Ky.: Ford Escape
- Chicago Assembly Plant, Chicago: Ford Taurus, Ford Police Interceptor, Ford Explorer
- Oakville Assembly, Oakville, Ontario, Canada: Ford Edge, Ford Flex
In 2014, Ford will launch dirt detection technology at the following plants:
- Flat Rock Assembly Plant, Flat Rock, Mich.: Ford Mustang, Ford Fusion
- Kansas City Assembly Plant, Claycomo, Mo.: Ford F-Series
No comments:
Post a Comment